Vibration testing is a vital tool used in the engineering and scientific world to ensure that structures, products, and components can withstand various forces. It involves subjecting materials to varying levels of vibrational force to gauge their strength, durability, and reliability under dynamic conditions.
Vibration tests can be conducted on anything from bridges or buildings to medical devices or spacecraft. This type of testing is essential for ensuring safety, quality assurance, and performance standards are met throughout all stages of development.
Understanding why vibration testing is important can help engineers create more effective designs and improve the overall functionality and longevity of any product or structure they produce.
What Is Vibration Testing?

Vibration testing is an important part of product development and validation. It involves subjecting products or components to vibration, shock, or other mechanical loads to simulate real-world conditions that the item may experience throughout its life cycle.
Vibration tests can reveal whether a product meets safety standards and will withstand wear over time as well as identify any potential issues with design or manufacturing processes before it goes into production. This type of testing typically takes place in a manufacturer’s facility using specialized equipment designed to replicate various types of force, such as those experienced during transportation, storage, field use, or even from natural disasters like earthquakes. By seeing how an object responds under these stresses, manufacturers can determine if their products are safe for consumers and ensure they meet performance expectations when on the market.
Reasons for Conducting Vibration Testing
Conducting vibration testing is an important step for any product that is designed to operate in harsh environments. Vibration testing can expose weaknesses or flaws in the design of the product before it goes into full production, saving time and money.
Additionally, vibration tests can simulate conditions that would otherwise be hard to replicate – such as high-altitude flight or hazardous terrain – so manufacturers can understand how their products will fare under such circumstances. Finally, vibration tests are a great way of ensuring quality control and compliance with industry regulations, making sure that each manufactured unit meets safety standards.
Benefits of Performing Vibration Tests
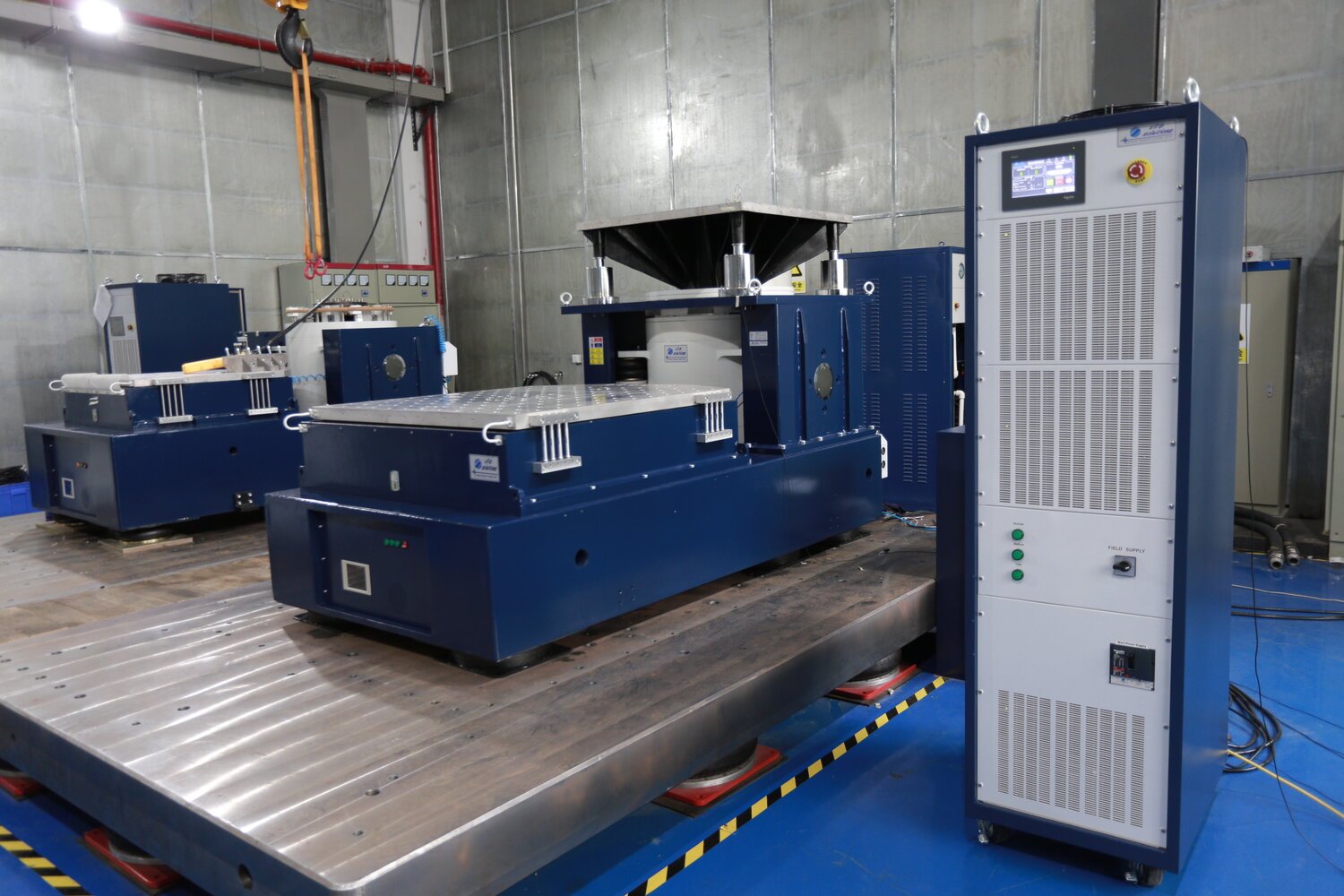
Performing vibration tests can be incredibly beneficial for a variety of reasons, from ensuring the safety of structures and equipment to detecting faults within complex machinery. Vibration tests allow engineers and technicians to detect issues that may not have been visible otherwise, saving organizations time and money in the long run.
For example, it is possible to use vibration testing to assess how much wear has taken place on parts or components over time, allowing users to identify when repairs or maintenance are necessary before a fault occurs.
Conclusion
Vibration testing is an important technique for understanding the performance and reliability of a product. It can provide invaluable information to engineers, manufacturers, and end-users regarding how products will perform in real-world conditions.
By simulating various environmental factors such as temperature, humidity, or pressure it allows them to determine if their product meets standards before releasing it. As technology advances and more complex products require extensive testing procedures, vibration testing will become increasingly vital for ensuring quality assurance across industries.
To learn more about this process and its importance in today’s world, consider researching further into vibration testing.